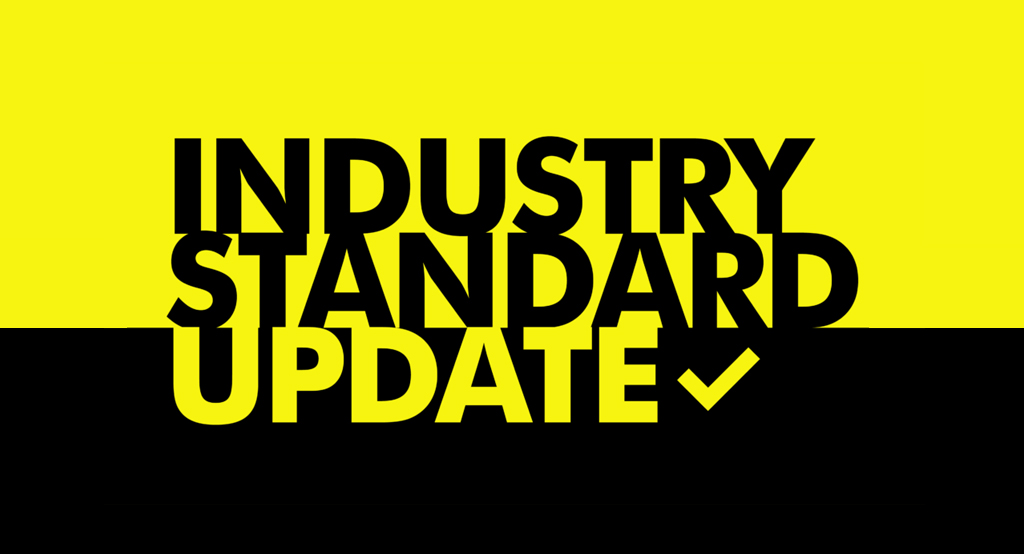
Industry Standard Update 085
IGEM/UP/11 Gas installations for educational establishments
Date issued: August 2018
This Industry Standard Update provides an overview of the recently published revised Industry Standard IGEM/UP/11 Edition — Gas installations for educational establishments, and highlights areas of significant change that the revisions have introduced.
Introduction
During August 2018, IGEM published a revision to IGEM/ UP/11(1). IGEM/UP/11 (Communication 1821)(2) supersedes Edition 2 (Communication 1744), which is now obsolete.
The revision to this standard comes into effect immediately.
To allow registered businesses time to carry out internal update training to reflect the technical requirements of the amended Standard, Gas Safe Register will inspect to the new requirements of this standard from 1 November 2017.
However, this should not restrict businesses from applying the specification sooner.
The following is a brief overview of the amendments made to IGEM/UP/11.
General
The standard provides guidance on the design, installation, operation and maintenance of gas installations for educational establishments.
References to legislation and current standards have been updated throughout.
Section 1: Introduction
Clause 1.12 has been added to provide guidance on the principles of risk assessment and makes reference to the Dangerous Substances and Explosive Atmospheres Regulations (DSEAR)(3).
Section 2: Scope
This standard covers:
- Piped gas supplied from gas distribution systems such as a NG distribution system or a LPG central bulk storage system
- Piped gas supplied through independent LPG supplies, eg, either a cylinder or an individual bulk storage vessel
- Portable LPG systems and appliances
- Portable temporary LPG heaters.
Section 5: Location and selection
Appliances and associated equipment/controls shall be selected such that they are suitable and safe for their operation and maintenance, and shall be located in rooms/ spaces that are suitable and safe for their operation and maintenance.
Type A and Type B space or water heating appliances shall not be located within a teaching area. Type C appliances used for space or water heating should not be located within a teaching area, unless suitably protected from interference and foreseeable damage.
The construction of any surface to which appliances are to be mounted shall be capable of withstanding the weight of the appliances and any ancillary equipment when in use. The surface on which appliances are mounted, and those surrounding the appliance, shall be able to withstand any excessive temperatures that may be generated by appliances when they are in use.
Section 6: Gas pipework
Clause 6.1 states that gas system operating pressures shall not exceed 50mbar except in special circumstances, such as for specialised experimental equipment, or where LPG cartridges are used. Where this is the case, a risk assessment covering the safe provision of gas shall be carried out.
When sizing pipework, if it is proposed to make allowance for diversity of usage, it shall be evaluated to ensure safety in the event of all appliances being used at once, and that they all continue to operate safely.
Clause 6.3 provides guidance that LPG cylinders (other than cartridges) should not be located within the building, unless they have been installed in a sealed and fire-protected compartment located on/within the outer building wall, that is accessible only from outside the building, and naturally ventilated solely to outside the building.
Sufficient purge points shall be installed. Any purge connection should be of at least the size stated in IGEM/UP/2(4), but shall be a minimum 12mm nominal bore (NB) and at least 25 per cent of the main pipe size. They shall be of sufficient size to enable purging to be undertaken in accordance with the procedures outlined in IGE/ UP/1(5), IGE/UP/1A(6), IGEM/ UP/1B(7) or IGEM/UP/1C(8).
Appliances that are required to be moved from time to time, eg, for cleaning, shall be connected using a flexible appliance connector, a self-sealing plug/socket complying with BS EN 15069(9) and one of the following methods, as appropriate:
- A flexible hose complying with BS 669-1(10) for domestic cooking appliances used in food technology settings
- A flexible hose complying with BS 669-2(11) for domestic and commercial equipment in a catering training setting
- A flexible hose complying with BS EN 14800(12).
Lightweight, readily moveable appliances such as laboratory Bunsen burners, hand torches, small boiling rings, etc, that are fitted with a connection designed to accept flexible tube by the manufacturer, and which are operated under continual supervision, may be connected to the gas supply using flexible rubber tubing, under the following conditions:
- The tubing shall be as short as is reasonably practicable and not exceed 1.0m long
- Such tubing may only be used when connecting to a bench-top type laboratory tap
- Where the outer diameter of the tube is 8mm or greater, the tube shall be secured using a crimp, or swaged, or worm-type clip, provided that the pressure does not exceed 50mbar. Crimp or swaged-type clips shall be applied for pressures exceeding 50mbar for all hoses.
Flexible tubing used in accordance shall be subject to regular inspections, and replaced after five years’ service, or before if showing signs of:
- Physical damage
- Environmental deterioration
- Failure such as blistering, soft spots, etc.
Section 7: Isolation of gas pipework and appliances
Where an AIV is required in the gas supplies to teaching areas which have appliances that are not fitted with flame safeguards, an automatic means of proving that downstream valves of the burners/appliances are closed shall be fitted. Figure 7 provides an example of a weep by-pass proving system. This proving system should not supply more than one teaching area. The system shall be such that it can only be reset by authorised persons.
A means to stop the system in an emergency shall be positioned near the teacher’s desk/board and either next to main light switches or at the exit from the room. The stop device may need to be shielded unless in a protected position.
Notes 1 and 2 have been added to Clause 7.2.5.3 to provide risk assessment guidance.
Where a risk assessment identifies that there is a risk of combustion products passing from a boiler room/enclosure/ space into an occupied space such as a teaching area/ corridor/office, a CO detection system shall be installed in the occupied area. The CO detection system shall raise an alarm and isolate the fuel supply. CO detection systems shall comply with BS EN 45544:3(13)
Section 8: Laboratories
Clause 8.1.11 states that, for fume cupboards, a risk assessment shall be performed to ascertain whether the gas supply and extract system needs to be interlocked.
Equipment shall be stored, sited, operated and maintained in accordance with the manufacturer’s instructions.
LPG cartridges shall only contain commercial butane or commercial propane, or mixtures thereof, and shall be of a type incorporating a self-sealing threaded connection. Pierceable cartridges shall not be used. LPG cartridges shall not exceed 0.45kg capacity.
- LPG cartridges shall be checked for leakage before being stored and before use
- Blowtorches shall only be used in safe locations and shall only be disconnected (eg, to change burner nozzles or replace cartridges) by, or under the supervision of, a competent person, and only in a well-ventilated area away from sources of ignition
- LPG cartridges shall be stored in a ventilated cabinet of non-combustible materials with at least 30 minutes’ fire-resisting construction, secured in position and kept locked
- Storage should preferably be located outside the building, and shall be adequately ventilated at both high and low levels directly to outside, and have explosion relief provision or gas leakage detection alarms. Stored cartridges shall not exceed 7.5kg in total, and shall not be stored in the same space as flammable materials or liquids
- Burners directly attached to gas cartridges shall be removed to secure storage after use in a place which is:
-
- Secure (eg, locked)
- Well ventilated
- Away from sources of ignition, combustible materials and escape routes
- In a safe position and a fire-resistant structure.
During holiday periods, gas cartridges shall be removed to secure storage.
LPG cartridges shall be checked for leakage after use. User-refillable LPG blow torches/burners shall only be refilled by competent persons, and in the open air away from any ignition source. Protective clothing and eye protection shall be worn as advised in the manufacturer’s instructions.
8.2.2: Mobile LPG benches
Gas pipework within a bench shall be located such that it is not exposed to damage when in use. Pipework shall either be metallic or flexible tubing (not exceeding 500 mm in length), conforming to BS 3212(14), BS EN 1763-1(15) or BS EN 16436-1(16), and secured with permanent clamp-type fittings.
Where gas storage is located within the bench:
- To be located within a separate enclosure
- An LPG leakage alarm shall be located at low level within the bench
- Ventilation shall be fitted in the base, and the top of the cupboard, each of 200cm2
- Combustible/flammable materials shall not be stored within the bench
- The bench supplier shall provide detailed instructions on routine inspection and/or replacement of flexible tubing within the bench.
Clause 8.2.2.3 states that LPG cartridges should be securely mounted on the outside of the bench and protected from damage.
Section 11: Installing appliances
The installation of gas appliances shall be in accordance with the manufacturer’s instructions and any relevant standards.
Where CO detector systems are installed, they shall comply with BS EN 45544:3. CO detection shall not be regarded as a means to negate the obligation of the educational establishment to ensure appliances and flues are maintained so as to ensure an acceptable level of performance and safety.
Section 12: Ventilation and flues
Purpose-provided permanent ventilation shall be fitted to provide sufficient fresh air for combustion and control of the indoor environment where gas appliances are used for educational purposes. When gas-fired appliances are in use, CO2 levels should not exceed 2800ppm.
A Note has been added to Clause 12.1.2 to provide guidance on what carbon dioxide shall comply with. High levels of CO2 in spaces containing gas-fired appliances shall cause a visual or audible alarm at 2800ppm. In addition, for new and refurbished installations, high levels of CO2 shall shut down the gas supply/appliances at 5000ppm. Staff should be trained in the operation of the CO2 monitor and be aware of appropriate action to take in the event of alarm activation.
Where mechanical ventilation systems are used, the type of interlock for shut down purposes depends on the type of gas appliances installed, and should be chosen in accordance with the guidance in IGEM/UP/19.
Flues
Where a horizontal or vertical flue passes through a teaching/occupied area, a CO detection system shall be fitted and designed to cause an alarm condition.
Food technology
The ventilation system shall be designed and operated to ensure that, under normal conditions, with appliances operating the teaching environment, levels should not exceed 2800ppm of CO2 at 1.5m above floor level. A visual or audible alarm shall activate at levels greater than 2800ppm, and shall cause an automatic shutdown of the gas supply at 5000ppm. Where multiple domestic or catering appliances are installed in a vocational training area, the ventilation shall comply with BS 6173(17), and shall be interlocked as specified in IGEM/UP/19(18).
Science laboratories and practical spaces – additional requirements
Ventilation systems shall be able to dilute combustion exhaust gases to an acceptable level.
In the majority of laboratories and preparation rooms, some form of mechanical ventilation will be required, at least some of the time, to deal with pollutant loads, the heat gain and water vapour produced by Bunsen burners as well as other equipment and solar gains.
To provide guidance on the minimum exhaust rates for science and practical spaces, Table 2 has been included in Clause 12.4.2.
Section 13: Electrical supplies and wiring
Any appliance that needs to be moved for cleaning shall be connected using plugs or sockets.
Section 14: Testing, commissioning and maintenance
Tests shall be performed on a planned basis to verify that the desired levels of CO2 are being achieved.
Exhaust systems (other than flues within chimneys) shall be subject to regular detailed inspection and service (typically annually, and at least every 14 months), to ensure no gas leakage and that the system is working correctly.
A risk assessment shall be prepared to meet the requirements of DSEAR.
Ambient conditions should be tested using a suitably certified and calibrated gas analyser.
Section 16: Emergencies
Teaching establishments shall prepare an emergency procedure to deal with gas incidents.
Bibliography
(1) IGEM/UP/11 Edition 3 Gas installations for educational establishments (Communication 1821)
(2) IGEM/UP/11 Edition 2 Gas installations for educational establishments (Communication 1744)
(3) Dangerous Substances and Explosive atmospheres Regulations 2002 (DSEAR)
(4) IGEM/UP/2 Edition 3 Installation pipework on industrial and commercial premises (Communication 1771)
(5) IGEM/UP/1 Edition 2 Strength and tightness testing and direct purging of industrial and commercial gas installations (Communication 1716)
(6) IGEM/UP/1A Edition 2 Strength testing, tightness testing and direct purging of small industrial and commercial Natural gas installations (Communication 1717)
(7) IGEM/UP/1B Edition 3 (with amendments October 2012) Tightness testing and direct purging of small Liquified Petroleum Gas/Air, Natural Gas and Liquified Petroleum Gas installations (Communication 1759)
(8) IGEM/UP/1C Strength testing, tightness testing and direct purging of Natural Gas and LPG meter installations (Communication 1751)
(9) BS EN 15069 2008 Safety gas connection valves for metal hose assemblies for domestic appliances
(10) BS 669-1 1997 Flexible hoses, end fittings, and sockets. Specification metallic flexible hoses for domestic appliances
(11) BS 669-2 1995 Flexible hoses, end fittings and sockets. Specification for corrugated metallic hoses for catering appliances
(12) BS EN 14800 2007 Corrugated safety metal hose assemblies for domestic appliances using gaseous fuels
(13) BS EN 45544-3 2015 Workplace atmospheres: Electrical apparatus used for the direct detection and direct concentration measurement of toxic gases and vapours. Performance requirements for apparatus used for general gas detection.
(14) BS 3212 1991 Specification for flexible rubber tubing, rubber hose and rubber hose assemblies for use in LPG vapour phase and LPG/Air installations
(15) BS EN 1763-1 2001 Rubber and plastics tubing, hoses and assemblies for use with commercial propane, commercial butane and their mixtures within the vapour phase. Requirements for rubber and plastics tubing and hoses
(16) BS EN 16436-1 2014 + A1 2015 Rubber and plastic hoses and assemblies for use with propane and butane and their mixture in the vapour phase.
(17) BS 6173: 2009 Specification for installation and maintenance of gas-fired catering appliances for use in all types of catering establishments (2nd and 3rd family gases)
(18) IGEM/UP/19 (With amendment January 2015) Design and application of interlock devices and associated systems used with gas appliance installations in commercial catering establishments (Communication 1777).
Summary
As previously stated, this Industry Standard Update is only a brief overview of the information contained in the amended standard. Registered businesses should be aware that they have a responsibility to ensure that they are fully apprised of all of the requirements of the whole published standard and its practical application.
Download Industry Standard Update 085 here: Industry Standard Update 085.