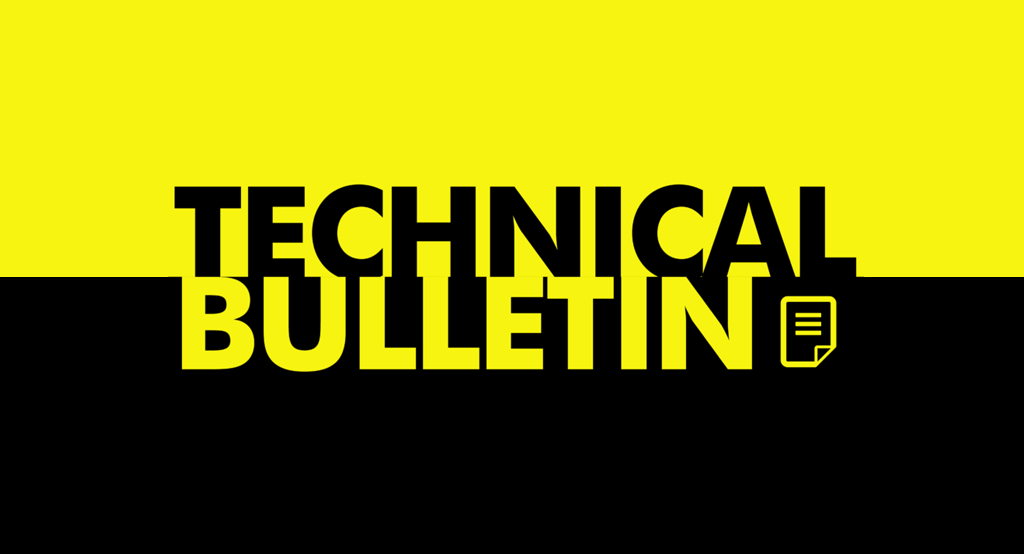
Technical Bulletin 059 – Potential gas escapes on stainless steel pliable or semi-rigid gas meter connections
Gas Safe Register has been made aware of a number of instances of work being undertaken around gas meters and where corrosive substances such as (but not limited to) flux and washing-up liquid have been allowed to come into contact with the stainless-steel/semi-rigid connection. In order to raise awareness of this, registered businesses should be aware of the information contained in this Technical Bulletin.
Introduction
This Technical Bulletin highlights concerns about a significant number of pliable or semi-rigid gas meter connections that are corroding for a number of reasons, resulting in gas escapes.
Possible causes of corrosion
The use of solder flux – used in the process of soldering gas/water pipework joints. Flux residue is allowed to drip on to the pliable meter connection and solidifies in the undulations of the corrugations during installation. Fluxes contain corrosive substances that will react with the stainless steel pliable connection, causing corrosion to take place in the form of pinholes. This reaction can occur within a very short period of time.
The use of washing-up liquid – or similar detergent-based product as leak detection fluid (LDF) can also have corrosive effects on corrugated stainless steel. Many commercially available washing-up liquids contain substances that are potentially corrosive to this material. Examples of the corrosion problem are shown in Figures 1 and 2.
Methods to reduce the corrosion problem
British Standard 6891(1) Clause 7.2.3 states: “It is important that pliable corrugated (stainless-steel) tubing is not contaminated in any way with flux or solder, either internally or externally.
Any soldering on adjacent copper pipework shall be completed, and the soldered component thoroughly cleaned of flux, before any connection to pliable corrugated (stainless-steel) tubing is made.”
IGEM publications IGE/UP/1B(2) and IGEM/UP/1C(3) provide guidance on the use of LDF. In particular, both standards require that: “Only proprietary leak detection fluids shall be used. LDFs containing more than 30 parts per million of halogens shall not be used on stainless steel components. LDFs containing ammonia shall not be used on copper or brass components.”
Guidance
Where there is the possibility of flux coming into contact with the corrugated stainless steel, it is recommended that the stainless steel connection should be appropriately covered with a dust sheet or similar during the soldering process to ensure its protection.
Where a soldered joint is being made within the vicinity of any corrugated stainless steel pipework, all excess fluxes and any residue will need to be completely removed from the soldered joint and on any corrugated stainless steel pipework/connections in the vicinity of the soldering activity.
The same requirements apply to the use of any propriety LDF – ensure that any fluid is completely wiped off joints and any corrugated stainless steel pipework in the vicinity after tightness testing is completed. Washing-up liquid or similar detergent should not be used for any testing purposes.
Note 1: While this TB relates to pliable meter connections, the same principles also apply to the installation of pliable/corrugated stainless steel supplies manufactured to BS 7838(4)
and/or BS EN 15266(5) or
other similar products.
Note 2: For details of current gas safety legislation, building legislation and industry standards for the geographical areas covered by Gas Safe Register, see the Legislative, Normative & Informative Document List (LNIDL)(6).
Note 3: For general information about the process behind the development of Gas Safe Register Technical Bulletins and the expectations for all Stakeholders, see TB 1000(7).
Bibliography
(1) BS 6891: 2015 Specification for the installation and maintenance of low pressure gas installation pipework of up to 35mm R(1¼)
(2) IGE/UP/1B Edition 3 – Tightness testing and direct purging of small Natural gas installations
(3) IGEM/UP/1C – Strength testing, tightness testing and direct purging of Natural Gas and liquefied petroleum gas meter installations
(4) BS 7838 – Specification for corrugated stainless steel semi-rigid pipe and associated fittings for low-pressure gas pipework of up to DN 50
(5) BS EN 15266 – Stainless steel pliable corrugated tubing kits in buildings for gas with an operating pressure up to 0,5 bar
(6) LNIDL – Gas Safe Register Legislative, Normative & Informative Documents List
(7) TB 1000 – An introduction to Gas Safe Register Technical Bulletins