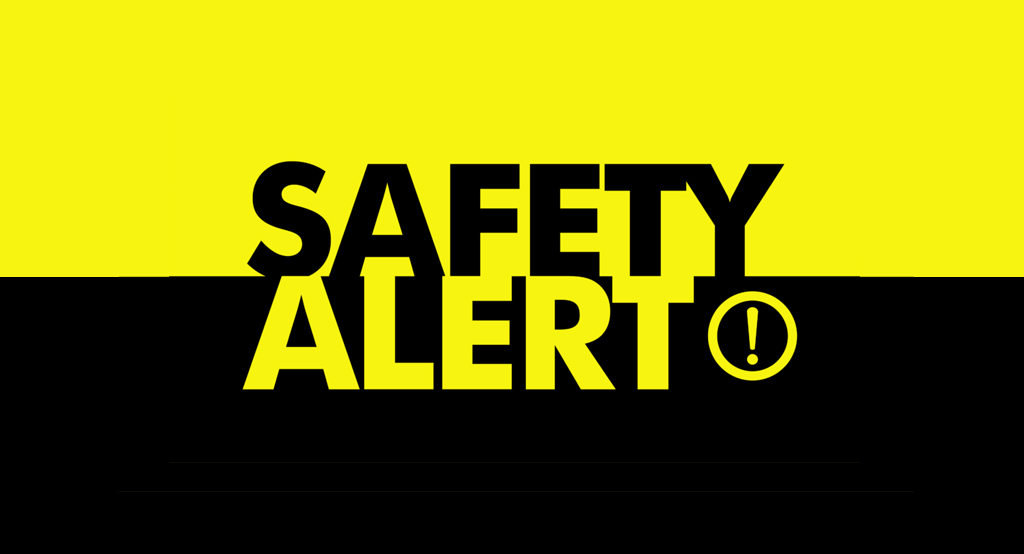
Safety Alert 023
Waterford Stanley Twin Series gas cookers
Date issued: May 2017. Developed with Waterford Stanley.
Introduction
This Safety Alert has been developed with Waterford Stanley to emphasise that the pressure switch settings on the Waterford Stanley Twin Series gas cooker, manufactured between 1996 and 2003, are a safety-critical factor and must be checked and set in accordance with the procedure detailed in this Safety Alert. The appliance has two pressure switches, either of which can detect a blocked flue.
Background
The Waterford Stanley Twin Series gas cooker operates with a dual blown gas burner arrangement and has been designed so that both fitted fans will operate even if only one burner of the two is operating/firing.
The design adds to safety of the appliance by preventing the re-circulation of products of combustion (POC) when a single burner is in operation. Due to the appliance design, there is a potential risk that a fault will remain undetected should both burner pressure switches simultaneously remain in the air proven position. It is therefore essential that engineers working on these appliances know how to check the pressure switch settings and functionality when they visit any appliances of this design, and that these checks are performed at each visit.
Affected models
Two Waterford Stanley range cookers are affected:
- Twin Series Gas Fired 100k
- Twin Series Gas Fired 80k.
Safe setting procedure for pressure switches on Twin Series gas cooker
When working on a Twin Series Gas range cooker, it is necessary to confirm that the pressure switch contacts have not become seized or bridged together. This is confirmed by removing the positive pressure air hose from the boiler pressure switch while the boiler burners are running. The burner must lock out immediately to verify the correct operation of the pressure switch. Repeat the procedure for the oven burner to verify the operation of the oven burner pressure switch.
If the burner continues to operate with the positive air hose removed, it signals that the pressure switch has become seized or bridged and must be replaced. Where it is not possible to replace the pressure switch, the current Gas Industry Unsafe Situations Procedure (GIUSP) should be implemented and the appropriate actions and warning notices/labels completed and issued.
Note 1: The GIUSP (TB 001) can be viewed by logging into your online account at: https://www.gassaferegister.co.uk/sign-in/
To ensure the safe and correct operation of the pressure switch, it must be set at between 0.25mbar and 0.3mbar below the pressure created in the burner. In the event of a blocked flue, the differential pressure in the burner should fall because of a pressure build-up in the appliance, resulting in a safe shut-down of the appliance. Under normal operating conditions, there will be a high differential pressure between the positive and negative connections on the pressure switch. This is caused by the operation of the fan on the positive hose and subsequent suction on the negative side. In the event of a blocked flue, there will be a lower differential pressure than would be expected.
Due to the blockage, there will be little change on the positive side (due to continued fan operation) but on the negative side there will be less suction and thus the differential pressure between the two will be lower. In some cases, the differential pressure will fall below a set level that will activate the pressure switch. However, if the pressure switch has not been set correctly (too low), the appliance may fail to shut down.
Prior to setting the pressure switches, establish that there is no pre-existing blocked flue condition.
Note 2: The Gas Safety (Installation and Use) Regulations 1998, Regulation 26(9) requires that after ‘work’ has been undertaken on an installed appliance, registered engineers need to undertake the necessary checks and tests to ensure that the appliance and any associated chimney/flue, is safe for continued use. In particular, and as a minimum they will need to check:
A. The effectiveness of any chimney/flue
B. The supply of combustion air
C. Its operating pressure or heat input or, where necessary, both
D. Its operation so as ensure safe functioning.
Setting/checking the pressure switch
Note 3: All checks should be carried out with the cover plate for the burner compartment in place, as it may have a small effect on pressures within the burners.
- Prior to setting the pressure switch, you must first establish that there are no restrictions or debris in the flue/chimney that could potentially create a restriction. As a minimum, a flue flow test should be conducted to confirm the correct operation of the flue/chimney.
- Ensure a suitable cowl/ terminal is fitted to prevent nesting birds dropping debris into the flue.
- Ensure that there is adequate ventilation for supply of combustion air.
- With the BOILER burner in operation, conduct a combustion analysis and confirm that the air setting on the burner is correct to achieve satisfactory combustion of approximately 9.5-10 per cent CO2 when measured at the boiler combustion test point at the rear of the cooker top behind the hotplate covers. Setting of the air adjuster may be required to correct CO2 readings, if no other gasrelated or flue defects are present (photo 1)
- While the BOILER burner is in operation, the boiler pressure switch should be increased slowly to detect the switching point. The burner control box should lock out, and the burner extinguish, to confirm that contacts are operating correctly. The boiler pressure switch should then be set to between 0.25-0.3mbar below the switching point. If the boiler pressure switch set point is below 1.5mbar, this indicates that there is undiagnosed problem which must be resolved (photo 2). Where it is not possible to repair or resolve the problem, the current GIUSP should be implemented and the appropriate actions and warning notices/labels completed and issued.
- Following the above checks, with the OVEN burner in operation, conduct a combustion analysis and confirm that the air setting on the burner is correct to achieve satisfactory combustion of approximately 9.0-9.5 per cent CO2 when measured at the oven test point on the hotplate. Setting of the air adjuster may be required to correct CO2 readings, if no other gasrelated or flue defects are present (photo 3).
- With the OVEN burner in operation, the OVEN pressure switch should be increased very slowly to detect the switching point. The burner control box should lock out, and the burner extinguish, to confirm that the contacts are operating correctly. Then the OVEN pressure switch should be set to between 0.25-0.3mbar below the switching point. If the oven pressure switch set point is below 1.8mbar, it indicates that there is undiagnosed problem which must be resolved (photo 4). Where it is not possible to repair or resolve the problem, the current Gas Industry Unsafe Situations Procedure (GIUSP) should be implemented and the appropriate actions and warning notices/labels completed and issued.
Download the Safety-Alert-023.pdf here