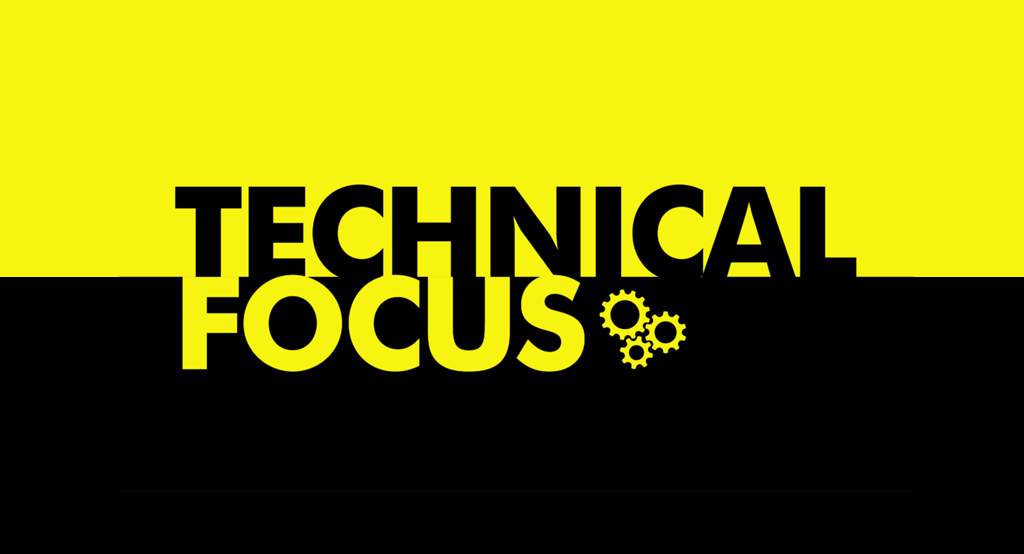
Open-flued laundry appliances
This article was originally published in Registered Gas Engineer’s November 2021 issue.
Open-flued non-domestic laundry appliances are less common on the high street than they used to be. But many can still be found in care homes and commercial laundries. Gas Safe Register Technical Support Officer Darren Pullin looks at the main safety considerations when installing and servicing them.
Gas Safe Register would like to thank Steve Hunter, technical training officer at WashCo, for additional information and the photos in this article.
A significant update to the standard covering the installation of non-domestic open-flued laundry appliances is that any dry-cleaning machine must be situated at least 5 metres away and make-up air must not come from that location. This is because the interaction of dry-cleaning chemicals and the laundry appliance’s burner flame can produce toxic gases. Neither should laundry appliances be sited in the same room as a bath or shower, and, of course, they should be installed in line with the manufacturer’s instructions.
Note: Always consult the manufacturer for specific guidance where dry-cleaning machines are installed.
Manual isolation valves
Manual isolation valves shall be provided to each laundry area, and sited next to the exit in a readily accessible location so as to enable safe isolation in the event of an emergency. A pressure test point shall also be provided as near as practicable downstream of the valve.
Interlocks
Interlocks shall be used to shut off/isolate the gas supply to the appliance by automatic isolation valves. They must be installed so that they are operated by emergency stop button(s) or a safety control in an emergency. Warning notices or signs must be fixed alongside manual emergency isolation valves and automatic isolation valve reset points, and must state what actions are needed before restoring the appliances.
Final gas connections to the appliance shall be flexible, in accordance with appropriate standards and the manufacturer’s instructions. They shall be sized to maintain the heat input and suitable for the type of gas used. The appliance must have a restraining device to prevent any undue stress or force from damaging the flexible connection.
Electrical connections
Electrical connections must conform to British Standards, depending on the type of connection and isolation method used. If there is a risk of mechanical damage, then braided, armoured, flexible or abrasion-resistant cable should be used. The point of connection to the mains supply shall be readily accessible and located adjacent to the appliance(s).
Make-up air
Make-up air is vital for the safe use of the appliance. Section 10 of BS 8446 states that exhaust terminals shall be at least 2,000mm from any openings or fresh air inlets to the building.
This is to ensure that make-up air is not contaminated by damp, warm air being re-circulated. All fans shall be installed so they do not adversely affect the safe operation of the appliance in the room or adjacent rooms, and make-up air fans shall be interlocked (with a manual reset) to the gas supply. In all instances, the manufacturer’s instructions should be followed before referring to the table, as some manufacturer’s requirements may be less or more than shown in the table.
Note: The cross sectional area in cm2 has been corrected. The sizes given in the standard are incorrect.
It’s important to remember that updates to standards or normative documents do not necessarily mean that an existing installation is dangerous if they don’t comply with the new standard. When you are faced with an installation that does not comply with the updated document, you must risk assess the installation/appliance using good engineering judgement and follow guidance from the Gas Industry Unsafe Situations Procedure (GIUSP), IGEM/G/11.
Exhaust systems
Exhaust systems must comply with the following requirements:
- Discharge to the outside atmosphere
- Present a minimal resistance to flow
- Be of smooth bore metal construction, as short as possible, and with a minimum number of bends and changes of direction
- Include provision for internal access for cleaning and maintenance
- Capable of withstanding temperatures up to 80°C for tumble dryers and 180°C for rotary ironers.
New appliances being fixed to existing exhaust systems have these characteristics.
Flexible exhaust connections for tumble dryers must be installed to the manufacturer’s instructions, not exceed 500mm in length and should be able to withstand the maximum stated temperature of the exhaust system. The ductwork may need to have fire dampers fitted, if required by the local bylaws, regulations or the fire authorities. The duct must be increased in diameter to overcome the pressure losses and shall be interlocked with the gas supply.
Termination
The termination shall allow the exhaust and all its components to clear to the outside with no build-up of lint. It must have no filters, and prevent the ingress of the weather but not impair the operation of the laundry appliance(s). A minimum clearance of 300mm below the termination from ground level shall be provided.
Exhaust testing
Exhaust testing will follow on from a successful visual test. Carry out an airflow test using the following recommended method, as described in Clause 15 of BS 8446:
- With a cold duct
- Light a smoke pellet and place in the ductway at the laundry appliance
- Turn the appliance on without heat being operated
- Examine the duct and joints for leakage, ensure all the smoke exits from the terminal
- Worst-case scenarios should now be introduced: doors opening/closing and multiple appliances being switched on/off if more than one appliance is connected.
The ducting backflow pressure shall also be tested to verify that it is within the parameters of the manufacturer’s instructions. The exhaust duct should be tested within 500mm of the appliance (under normal working temperatures) and shall have an airflow pressure of less than 1.25mbar. During tests, any other exhaust systems to the room shall be operating at maximum. The laundry appliance shall be commissioned in accordance with the manufacturer’s instructions. This will include the ductwork and the correct operation of all safety controls, safety shut-off valves and pressure/flow sensing valves.
Other appliances and ventilation that may affect the safe operation of the laundry appliance(s) must be considered, again with worst-case scenarios introduced. If carbon monoxide alarm systems are fitted, they must conform to BS EN 45544-3: however, their installation does not negate the obligation to maintain appliances and equipment to acceptable levels. Gas engineers should provide instructions to the operator, as required under GSIUR, and these may include any wiring diagrams and programs created to support the operation.
Servicing and maintenance must be carried out in accordance with the manufacturer’s instructions, and there may also be a requirement under GSIUR to have the appliance included in an annual gas safety check if the property is tenanted.
Note: Employers and selfemployed people must have installations under their control maintained in a safe condition, to prevent the risk of injury. Service requirements must be indicated to the responsible person by the gas engineer, and gas work must be undertaken by a suitably qualified registered gas engineer.
Bibliography
BS 8446:2020: Installation and maintenance of open-flued, non-domestic gas-fired laundry appliances. Specification Industry Standard Update 099: BS 8446: 2020 Installation and maintenance of open-flued, non-domestic gas-fired laundry appliances – Specification
You can read ISU 099 by logging into your Gas Safe Register online account at www.gassaferegister.co.uk/sign-in