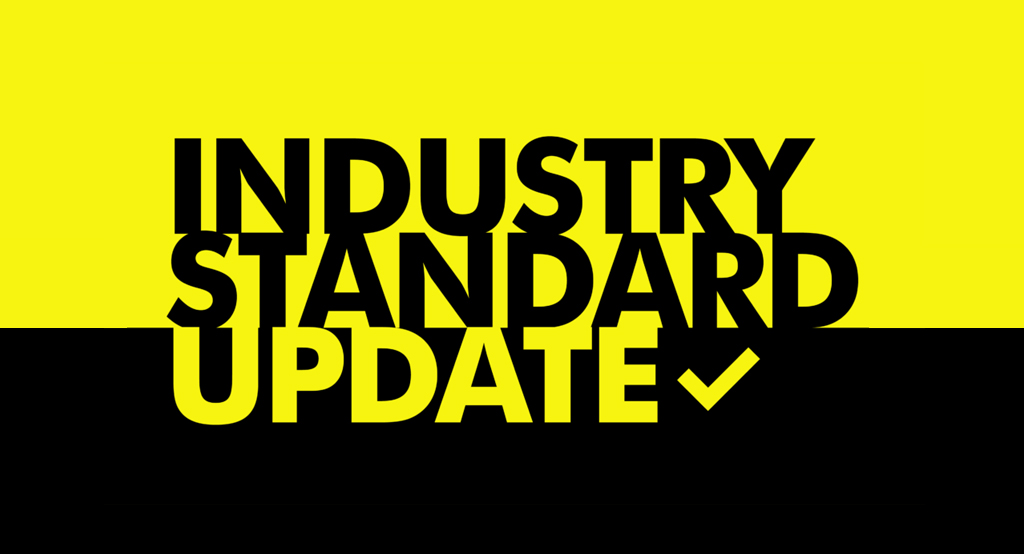
Industry Standard Update 100: IGEM/UP/6 Edition 3 Application of compressors to Natural Gas fuel systems
Date issued: 23 December 2020
This article appears in full in the February 2021 edition of Registered Gas Engineer.
This Industry Standard Update provides an overview of the recently published revised Industry Standard IGEM/UP/6 Edition 3 Application of compressors to Natural Gas fuel systems, and highlights areas of significant change that the revisions have introduced.
Introduction
During December 2020, IGEM published a revision to IGEM/UP/6(1). IGEM/UP/6(2) (Communication 1813) supersedes Edition 2 (Communication 1741), which is now obsolete. The revision to this standard comes into effect immediately.
To allow registered businesses time to carry out internal update training to reflect the technical requirements of the amended standard, Gas Safe Register will inspect to the new requirements of this standard from 1 April 2021. However, this should not restrict businesses from applying the specification sooner.
The following is a brief overview of the amendments made to IGEM/UP/6 Edition 3.
General
References to legislation and current standards have been updated throughout where required.
Section 2: Scope
IGEM/UP/6 covers the installation and operation of compressors, with outlet pressures in the range exceeding 0.5bar but not exceeding 400bar. IGEM/UP/6 applies to new construction and replacement of, or extension to, servicing, and maintenance of existing installations using compressors. It is not retrospective, but it is recommended that existing installations should be modified to meet this standard, when appropriate.
Section 4: Gas supply
Clause 4.1.1 provides guidance that the meter asset manager (MAM) shall be informed of the:
- Presence of a compressor, and associated equipment including receivers, pipework, etc
- Maximum volumetric flow and pressure lift
- The number and type of each unit of plant and, where available, the anticipated load pattern for each
- Estimate concerning any anticipated growth over the next 12 months
- Where necessary, for example during commissioning where testing may require peak flow, for a short period, that may exceed stated Qmax
- Maximum fault pressure that the compressor is capable of putting back on to the meter installation, MIPc (for example arising from sudden stop or reverse flow from the outlet)
- Desired inlet pressure.
The characteristics of the gas pressure at the outlet connection from the meter installation shall be obtained from the MAM, including possible variations:
- STPmi: strength test pressure
- MIPmi: maximum incidental pressure (fault pressure)
- MOPmi: maximum operating pressure
- SPmi: set pressure
- LOPmi: lowest operating pressure
- DmPmi: design minimum pressure.
Clause 4.1.5 states that when an unregulated meter installation is being considered, the GT must provide declared network pressures as follows:
- MIPu
- MOPu
- LOPu
- DmPu.
Note 3 has been added to Clause 4.6.1.2.1, which states that further information for NRVscan be found in IGEM/G/10(3).
Note 2 to Clause 4.6.1.4 states that the formula in the clause assumes that Pso = 1.
Section 6: Installation of a compressor
Gas compressors should not be located within engine enclosures or plant rooms unless permissible, subject to risk assessment and confirmation of hazardous zoning requirements for the particular plant involved.
A Note has been added to Clause 6.3.1.5 to advise that suitable warning signs may be used to discourage the storage of flammable products. Compressors should have an emergency depressurisation and venting system.
Clause 6.8.3 states that venting shall be to atmosphere via a vent stack of suitable height, exhausting to a safe location and taking into consideration the following:
- Should terminate preferably 3m above ground level and preferably 1m above roof level
- Vent pipes should terminate vertically upwards where practicable or vertically downwards
- Vents should not pass through electrical intake rooms, transformer rooms, lift shafts, or refrigeration chambers
- Vents shall be of permanent construction
- Vents should be straight and as short as practicable and shall be designed to prevent undue back pressure upon the relief valve
- Consideration shall be taken in the design of vent terminals to minimise the risk of blockage from foreign matter and ingress of water
- Vent system shall have adequate support to reduce stresses caused by the venting process
- When deciding on the location, consideration shall be given to the preservation of the environment, the impact on planned alterations, routing and termination of vents
- The hazardous area zone should not pass the outside of the customer’s boundary on to publicly accessible areas
- Ventilators shall not be located by or near any air intake duct.
Clause 6.8.10 states that the use of a flame arrestor is not recommended with NG compressors, although flame arrestors may be required with air/gas mixing machines. If a flame arrestor is fitted, the required flow capacity for the vent shall be maintained under all conditions and it shall be designed to encourage the safe dispersion of the releasing gas, and prevent the ingress of water, rain, snow, etc.
The siting of any vent termination shall result in a hazardous area classification at the point of discharge. Vent manifolding shall be permitted only where it can be shown that excess pressures, or adverse back pressure effects on other equipment, will not occur.
Guidance in Clause 6.8.13 states that vent pipework shall be designed for exhausting gas at high pressure and high velocity, by catering for the effects of erosion, excessive noise and reduction in temperature due to expansion of the gas. Table 2 has been included in Clause 6.13.2 to provide guidance on the minimum inspection and testing of steel welds for installation with a MOP exceeding 500mbar.
Clause 6.18.1 provides guidance on which safety features the electrical control system shall include in addition to motive power.
Clause 6.18.3 states that equipment interlocks shall be provided to ensure safety of operational staff and the operation of the compressor. This shall take account of the process interfaces with connected plant and equipment.
Further guidance on interlocks can be found in Clause 6.18.3.
Summary
As previously stated, this Industry Standard Update is only a brief overview of the information contained in the amended standard. Registered businesses should be aware that they have a responsibility to ensure that they are fully apprised of all of the requirements of the whole published standard and its practical application.
Bibliography
(1) IGEM/UP/6 Edition 2 Application of compressors to Natural Gas fuel system (Communication 1741)
(2) IGEM/UP/6 Edition 3 Application of compressors to Natural Gas fuel system (Communication 1813)
(3) IGEM/G/10 Non-return valves (Communication 1785)