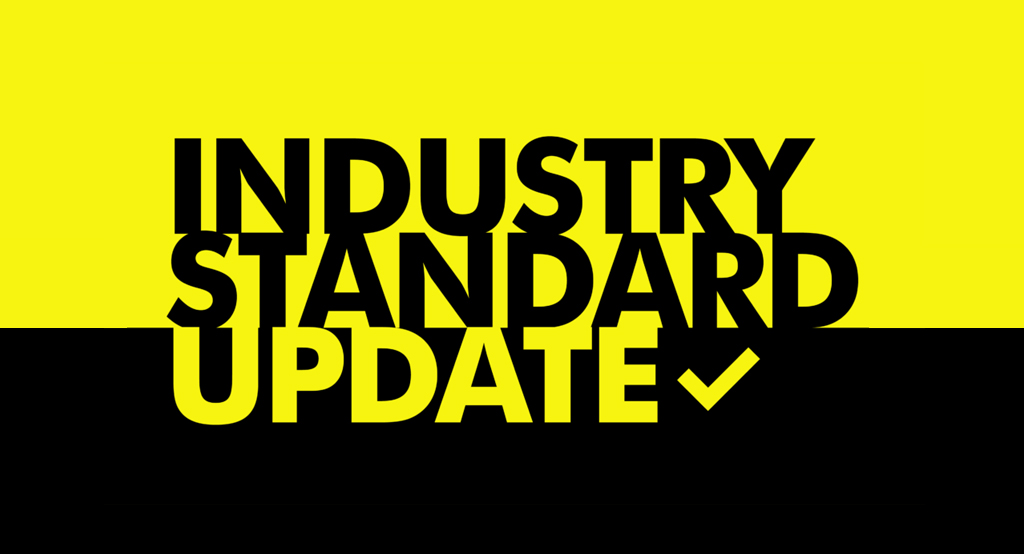
Industry Standard Update 098 – Liquid Gas UK CoP 22
This Industry Standard Update (ISU) provides an overview of the key areas of change arising from the revision of Liquid Gas UK Code of Practice 22 – 2020 Design, Installation and Testing of LPG Piping Systems.
Introduction
During June 2020, Liquid Gas UK published a revised Code of Practice 22 – 2020(1)– Design, Installation and Testing of LPG Piping Systems. This superseded the previous edition, published in August 2011 (with amendment 1 (corrigendum) February 2012)(2).
The revision to this standard came into effect in June 2020.Gas Safe Register will inspect to the new requirements of this Standard from 1 November 2020.
The following is a brief overview of the areas of significant change to the amended standard, Liquid Gas UK CoP 22.
General
Legislation, normative references and current standards have been updated throughout where necessary.
Scope
Liquid Gas UK CoP 22 sets out the guidance for:
- Steel pipework up to and including 150mm nominal bore
- Copper pipework up to and including 35mm outside diameter
- PE pipework up to and including 180mm outside diameter
- Composite pipework up to and including 150mm nominal bore
- Flexible hoses, tubing and associated assemblies up to and including 80mm nominal bore.
While primarily intended for static installations, the recommendations in this Code of Practice may be applied to mobile equipment, including
road tankers.
The Code of Practice applies to:
- New pipework
- Modifications and/or alterations to existing pipework
- Service pipework (as defined in the Gas Safety (Installation & Use) Regulations 1998 as amended(3)).
Section 3: Pipework design limits and materials
This section contains much of guidance that was provided in Section 2 of the previous edition.
Clause 3.2.5 states that for new installations, buried pipework operating at a nominal pressure >75mbar shall be run a minimum distance of 3000mm from buildings, except at the point of connection to the premises.
For further guidance, refer to Table 5 and Figures 1a and 1b.
Buried pipework operating at a nominal pressure of ≤75mbar shall be run a minimum distance of 250mm from buildings, except at the point of connection to the premises.
For further guidance, refer to Table 5 and Figure 2.
Table 5 and Figures 1a, 1b and 2 are new to this version of CoP 22.
Clause 3.2.6 provides guidance for existing buried pipework.
For existing buried pipework installations installed before the publication of this Code of Practice, where proximity distances are less than those given in Clause 3.2.5 (for the operating pressure), the buried pipework may continue to be operated in accordance with their existing inspection and maintenance strategy.
Where opportunities arise, such as modifications or repairs, the owner/operator should comply with Clause 3.2.5. If this is not practicable, the proximity distance does not need to be modified, subject to the inspection and maintenance strategy being reviewed and recorded by the pipework operator/owner to mitigate the risk of operating this pipework.
Where reasonably practicable, extensions to existing pipework installations should comply with Clause 3.2.5. However, for extensions to existing installations on caravan holiday home (CHH) and residential park home (RPH) sites, where a high degree of ventilation between the base slab and the CHH or RPH can be guaranteed either by no skirts or ventilation in accordance with HSE Research Report RR945, reduced proximity distances may be permitted.
Where this is not reasonably practicable and a documented risk assessment by a competent person concludes that the cost of compliance with these requirements is grossly disproportionate to the safety benefit gained, then the proximity distance for pipework operating at a pressure of >75mbar may be reduced, but it shall not be less than that required for pipework operating at ≤75mbar.
Section 3, Clause 3.2.7 provides guidance for additional emergency control valves (AECV) as well as emergency control valves (ECV).
Clause 3.2.8 provides guidance for above-ground entries into buildings. Figure 4 has been included in this Clause and above-ground entries or exits shall be installed in accordance with the principles shown.
Clause 3.2.9 provides guidance relating to below-ground entry/exit of pipework, with Figure 5 providing further clarification.
The following Figures have been included in this section:
Figure 6: Cylinder Installation, Standard Regulator
Figure 7: Cylinder Installation, Automatic Changeover
Figure 8: Bulk Vessel, 37mbar supply
Figure 9: Bulk Vessel, Property End Final Stage Regulator.
Section 5: Special requirements for pipework installed below ground level (buried)
Pipework should be laid at a sufficient depth to provide cover adequate for the likely superimposed loads. Where depth of cover alone is insufficient to protect against such a load, additional protection shall be provided.
Cover should not be less than:
- 600mm within private property and under tarmac or grass footpaths where there is no likelihood of heavy traffic, or
- 750mm under roadways and adjacent grass verges, and elsewhere
- 1100mm when passing through agricultural land.
Where it is not reasonably practical to achieve the depth of cover specified, then, subject to approval by a competent person, it may be reduced provided that the pipework is suitably protected. eg, by the installation of additional mechanical protection approximately 100mm above the pipe.
Figure 10 provides details of a buried pipework trench.
Ducts may be used where it is inconvenient or impractical to leave an open trench. Ducts should be coloured yellow and should be overlaid with gas marker tape and preferably should be perforated along their length.
Ducts shall have the same depth of cover as PE pipe. If ducting is to be laid around bends, the same bend radius as given for the PE pipe should be applied. A clearance of at least 250mm should be maintained between gas pipe ducting and the known position of other utilities’ plant being installed alongside or crossing the service. Where this cannot be achieved when crossing, other plant additional protection should be applied to the service.
For ease of insertion, the internal diameter of a duct should be sufficient to allow insertion of the pipe without damage. For excessive lengths of duct, the gas supplier should be consulted.
Ducting should terminate adjacent to the service pipework entry point, allowing sufficient room to assemble entry fittings.
Section 6: Hoses and hose assemblies
This section is new to the Code of Practice and applies to all types of hoses and flexible connection in use with both vapour and liquid LPG.
Hoses should comply with a standard ensuring they are acceptable for conveying LPG as vapour or liquid as required and for the service intended.
In this section, hose and hose assemblies refer to all types of flexibles unless otherwise specified.
This section provides guidance on storage, flexible connections, hoses and tubing for use with LPG vapour, hoses for use with liquid or at vessel vapour pressure, installation of hose assemblies, twisting and bending, protection, and hydrostatic protection.
Section 7: Pre-service, inspections, testing and commissioning
All pipework shall be inspected and, where necessary, tested under the following circumstances:
- For new installations, as part of the commissioning process
- For alteration to, replacement of, or re-use of, existing installations
- For new extensions to existing installations
- Prior to any work on existing installations
- Where there is a known or suspected gas escape or if there is a smell of gas
- Where there has been a complete loss of supply pressure, ie, upstream of the ECV, or of installation pressure
- For routine testing of existing installations
- Before purging of installations
- Before introducing gas
- Before re-establishing an existing gas supply.
The following pipework shall be purged into service after inspection and testing as part of the commissioning:
- For new installations
- For alteration to, replacement of or re-use of existing installations
- For new extensions to existing installations
- Where there is the possibility of extraneous air being present in the installation.
Where pipework is to be taken out of service temporarily or permanently, it shall be purged out of service in accordance with Section 8 and Appendix J.
The guidance in this section in relation to strength and tightness testing has been revised and aligns with the guidance provide in the IGEM/UP/1(4)series of documents.
Section 8: Purging
A satisfactory tightness test shall be completed immediately prior to a purge and admitting LPG into any pipework.
Purging shall be carried out in accordance with Appendix J, or an alternative recognised method such as IGEM/UP/1.
Purging of pipework systems should only be carried out by or under the supervision of competent persons. For installations subject to GSIUR, the competent person shall be an appropriately qualified Gas Safe registered engineer.
For larger pipework and systems, which include large volume items, eg, vaporisers, air-gas mixers, etc, the system should be purged before introducing LPG.
Purge gas should be introduced in a controlled manner using an adjustable pressure regulator.
During the introduction of LPG, it may be necessary to release any inert gas from the system. The gas should be released at a safe location and must not be allowed to accumulate in any confined space. A flare stack with permanent pilot and flame arrester may be used provided that it is adequately supervised and is located at a safe distance from the LPG storage vessel or other vulnerable structure.
If necessary, the introduction of LPG may be undertaken in sections provided that suitable purge gas release points have been provided.
Liquid pipework shall be purged to LPG vapour before admitting liquid LPG.
Section 9: Commissioning and records
A final leak check should be carried out in operating mode following commissioning using a proprietary leak detection fluid. Any leak detection fluid used to test pipework joints should be washed off with clean water at the end of the test.
Final checks of the working pressures should be carried out to ensure that the system is functioning correctly and vapour pressure at ECV checked to ensure it is within permissible limits.
Installations at commercial and industrial premises subject to the Health and Safety at Work etc Act(5)should include the necessity of developing an inspection strategy. For guidance refer to Liquid Gas UK User Information Sheet UIS15(6).
The following appendices have been included in this revision of CoP22:
- Appendix B: LPG Safety Data Sheets
- Appendix C: Legal Requirements
- Appendix G: Pipe Sizing, Regulators and Working Pressures
- Appendix H: Proprietary Pipework Systems
- Appendix I: Gas Tightness Testing of LPG Pipework
- Appendix J: Purging
- Appendix K: Guidance on Domestic LPG Metallic Underground Pipework (Liquid Gas UK Industry Information Sheet 033 (IIS033) ).
Bibliography
1. Liquid Gas UK Code of Practice 22 – 2020 Design, Installation and Testing of LPG Piping Systems. This supersedes the previous edition
2. Liquid Gas UK Code of Practice 22 – 2011 (Including amendment 1 (corrigendum) February 2012) – Design, Installation and Testing of LPG Piping Systems
3. The Gas Safety (Installation and Use) Regulations 1998
4. IGEM/UP/1 suite – Strength testing/tightness testing/direct purging of gas installations
5. The Health and Safety at Work etc Act 1974
6. UIS 15 Inspection and Maintenance of LPG Pipework at Commercial and Industrial Premises