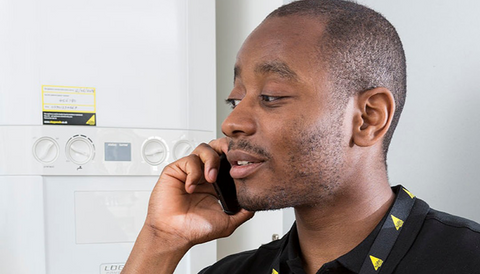
Guidance on dealing with low-pressure supply – IGEM/G/13
The new guidance document IGEM/G/13 – Domestic supply capacity and operating pressure at the outlet of the meter – provides clarity on the requirements of supply capacity and operating pressures (at the outlet of the meter) for domestic properties. Trevor Smallpeice, chair of the Low Pressure Supply Pressure Working Group, answers some of the questions that may arise from the new guidance and changes to working practices.
Why is there a new guidance document?
Incidents of low pressure should be dealt with safely, consistently, efficiently and effectively, and accepted by all parties to their satisfaction.
This would produce a:
• Limit on the nominal gas load for domestic premises in kW
• Mutually agreed pressure test point
• Harmonised procedures for installing appliances, covering pre-installation, commissioning and post-commisioning
• Procedures for responding to reports of low-pressure supply
• Methodology for reporting low-pressure supply
• Common approach for investigating low-pressure supply.
What should the capacity and pressures be and where should it be measured?
A standard domestic gas load (capacity) is capped at gross 65kW. However, any existing gas service is likely to have been designed for the demand appropriate to the property type and appliances when it was built. This means that you cannot assume that the existing service has been designed for a gas supply of 6m³/h (65kW).
Note: Requests for larger gas load should be made to the gas supplier/transporter.
The test point at the outlet of the meter installation is the point of common access to all parties. You should use the gas pressure measured at the outlet of the meter to determine the suitability of supply for the gas load of the premises.
The operating pressure of the outlet of the meter after a one-minute stabilisation should not be less than 18.5mbar and not more than 23mbar.
Can I find out what the domestic gas load is on a property where I am going to install a new appliance?
You can do this in two ways: carry out tests on the current supply if practicable and/or use the GT1 Process. These procedures are intended to establish that the gas supply is suitable for the intended new appliance(s) and if not, enable contact with the gas supplier and/or the gas emergency service provider (ESP) so that the issue can be resolved made before the appliance(s) is installed.
Therefore, before the gas engineer or installation designer decides what the customer and installation needs, the following pre-installation checks should be carried out to establish the existing gas supply. As soon as possible and if practicable (if appliances can be operated safely) operate all the appliances within the premises at a high operating load and take a reading to confirm that the outlet pressure of the meter after a one-minute stabilisation period is not less than 18.5mbar and not exceeding 23mbar.
High operating load is the maximum operating load for the entire gas installation in the premises for a period of high demand. To replicate this, operate:
– the highest output appliance (typically the boiler) at its maximum load. For combi boilers, this will be hot water demand to taps, in which case operate all hot taps at full flow
– all other appliances at 50 per cent load: for example, light two burners on a hob that has four burners.
The GT1 Process – Establishing the gas supply capacity of a domestic premises: to confirm the supply capacity, an application can be made to the gas supply company/gas transporter. Refer to GDN/PM/GT/1 Management procedure for requesting gas service pipe pressures and capacity information.
You can find the relevant forms here: search for GT1 Application, which will offer a download ENA GT1 form “Standard form for requesting information on pressure and capacity”. Complete the form and then apply to the relevant gas transporter, which will be Cadent, WWU, NGN or SGN. If the property is served by an independent gas transporter such as GTC, make the application to them.
What should I do if there is low pressure (below 18.5mbar) at the outlet of the meter when installing a new appliance or during servicing/maintenance?
Commissioning the appliance shall be undertaken in accordance with the manufacturer’s instructions. This confirms that the appliance is operating as specified by the manufacturer.
Verify appliance inlet gas pressure as per the manufacturer’s instructions: operate the installed appliance at maximum appliance load as specified in the commissioning instructions, eg, commissioning/chimney sweep mode.
After commissioning, an entire installation check is required: operate all the appliances within the premises at a high operating load and take a reading to confirm that the outlet pressure of the meter after a one-minute stabilisation period is not less than 18.5mbar and not exceeding 23mbar.
If the outlet pressure of the meter after a one-minute stabilisation period is less than 18.5mbar or more than 23mbar, report to the ESP using the “Reporting of Low Pressure” process.
If the appliance(s) has been commissioned, check the working pressure at the outlet of the meter installation and ECV by operating all the appliances within the premises at a high operating load and then take a reading to confirm that the outlet pressure of the meter after a one-minute stabilisation period is not less than 18.5mbar and not more than 23mbar.
If the outlet pressure of the meter after a one-minute stabilisation period is more or less, report it to the ESP using the “Reporting of Low Pressure” process.
First-call operatives
Throughout this process, you should understand the role of the ESP first-call operatives (FCOs):
• FCOs cannot work on or set up appliances
• FCOs will need the gas engineer to work with them to undertake all necessary checks and tests
• Job reports are a critical part of the process
• ESP FCOs and gas engineers should work together for an agreed and satisfactory outcome for the customer.
The gas engineer should wait for the ESP to attend whenever possible (this will be within two hours). Particularly if the appliance is new, the gas engineer should wait for the ESP or arrange to attend site with the ESP. Where it is not possible to wait, the gas engineer’s job report should contain:
• Confirmation that the internal pipework is sized correctly
• Working pressure measurements taken
• Any recent changes, eg, new appliances, meter position moved
• The installation’s total load.
The following actions are required, as appropriate:
• For an existing appliance, which affects the safe operation of any appliance – such as combustion and/or flame stability – the appliance shall be made safe in accordance with IGEM/G/11 (GIUSP).
• Where the installation is new, the appliance must be disconnected from the supply and sealed with appropriate fitting(s) in accordance with Reg 26(5) of GSIUR as an uncommissioned appliance.
Note: If this action is taken, the gas engineer will need to be available to enable the ESP engineer to undertake a joint investigation.
What will happen when the ESP attends – what is a joint investigation?
The ESP takes responsibility for investigating pressure issues and sharing the outcome of the investigation with the customer and gas engineer, as appropriate. The ESP will undertake tests in line with its company procedures as well as tests with the gas engineer.
If the appliance(s) are new and uncommissioned, provided that the gas engineer with appropriate competence is present on site, allow the new appliance(s) to be set up to operate in their commissioning mode. Then check the working pressure at the outlet of the meter installation and ECV by taking a reading to confirm that the outlet pressure of the meter after a one-minute stabilisation period is not less than 18.5mbar and not exceeding 23mbar.
Note: If the outlet pressure of the meter installation falls outside this range, and if necessary, in order to assist in finding the root cause of the problem, check the working pressure with appliances operating at normal and/or high operating load.
Normal load for the new uncommissioned appliance would be set to working on hot water demand to taps and/or heat demand.
If the appliance(s) has been commissioned, check the working pressure at the outlet of the meter installation and ECV by operating all the appliances at a high operating load and then take a reading to confirm that the outlet pressure of the meter after a one-minute stabilisation period is not less than 18.5mbar and not exceeding 23mbar.
Note: This may be at the time of an appliance service or maintenance visit.
The ESP may carry out further investigations, including the standard service six-minute average pressure test under high operating load conditions.
If the average working pressure over a six-minute period at the outlet of the ECV is unsatisfactory, and the problem is limited to a single property, the investigation should focus on the service pipe. Where problems are experienced at adjoining premises, or where there is any history of problems at adjacent properties, the ESP should consider the possibility of a wider underlying issue.
Where poor pressure in a wider vicinity is confirmed, the ESP will request support and start an investigation to determine the extent of the affected area by checking opposite and adjacent premises, and checking pressures at strategic locations in the surrounding area and extremities of the mains, as appropriate.
The low pressure could be for a number of reasons, such as water ingress into the service/main, network issues like faulty distribution regulators or extreme weather conditions. However, if the investigation suggests that the service is at fault, the ESP will explain to the customer, gas engineer or approved meter installer the actions to be taken, along with a likely timescale for resolution.
IGEM/G/13 is free to download here.
This article was also published in Registered Gas Engineer, September 2022.