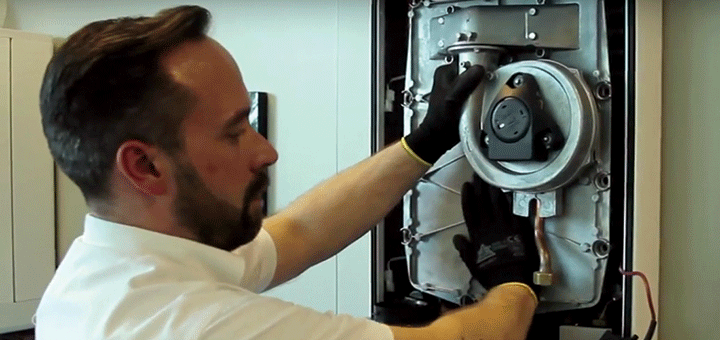
A guide to annual boiler servicing
What’s best practice for gas boiler servicing? Here, the HHIC’s consumer guide, published earlier this year, outlines agreed industry best practice.
Servicing the boiler
- Have the manufacturer’s instructions for the boiler to hand
- Operate the boiler briefly to ensure it appears to work correctly. Isolate the boiler/heating system electrically and confirm this with suitable test equipment. Check the fuse rating for the boiler/heating system is correct
- Remove the boiler case and visually inspect the appliance, internally and externally, for any signs of distress, such as corrosion or water leaks
- Clean the boiler and its components, including the primary heat exchanger, burner, and condensate trap, with due regard to the manufacturer’s instructions
- Safely reinstate the electrical supply. Carry out a check of the boiler’s gas burner pressure, a gas-rate check (taken at the gas meter), or both, where appropriate
- Visually check the flame picture (where visible) and carry out a flue gas analysis test
- Ensure any combustion analysis test points are correctly replaced, and any boiler case seals are forming an effective seal
- Check that any ventilation requirements for the boiler have been met
- Check the boiler chimney/flue throughout its length, including its point of termination. Carry out flue-flow and spillage tests (smoke tests) if the boiler is of an open-flued type
- Check that any boiler safety devices operate correctly Check there is no escape of gas from the boiler, or connecting pipework
- In the event of any safety defect(s) being noted, advise the customer of the details, and either rectify them, or act in accordance with the Gas Industry Unsafe Situations Procedure (GIUSP)
- Where rectification is not possible, discuss with the customer any remedial action required, and the options to correct the faults
- Complete the Benchmark service record, and provide any additional work documentation.
Top tip:
Try to find out the boiler’s make and model in advance so that you can download the manual before you arrive.
Final checks
- Check system controls for correct operation, and that both the central heating and hot water function correctly, if you have not already done so
- Walk the heating system, checking for any water leaks, signs of corrosion, and that all radiators heat evenly, bleeding any air present. Check any hot water storage cylinder for leaks, correct insulation, and any obvious defects. Check and clean system sludge/debris from any installed heating system filter
- For sealed systems, check that the final system pressure is in accordance with the manufacturer’s instructions
- If the customer is present when the service is completed, discuss the work carried out with them, and answer any questions they may have
- Where further work is required, explain what this is, why it is needed, and provide a quotation if requested, and if the work is not already covered by an existing contract. Where an additional visit is required, and if the customer agrees, endeavour to agree a suitable date and time for the appointment. When returning to carry out further work or repairs, ensure all relevant parts and materials are ordered for the job, and that these are as specified by the boiler manufacturer
- Check that the appliance and system control settings (eg, on/off times for the central heating, and thermostat settings) are as the customer requires or, if they are not present, are left as found
- If you have not already recorded information about the service directly in the Benchmark service record, add the relevant appliance readings and information, and record a short job report, including any parts fitted
- Advise the customer that continued regular servicing of their gas appliances is recommended, and that it is a condition of any ongoing appliance manufacturer’s warranty that gas boilers are serviced appropriately, at least annually, by a suitably qualified Gas Safe engineer.